Quality Inspection/Testing
PCB testing conducts various tests on printed circuit boards to verify their quality and performance, ensuring accurate elimination of any defects or issues that may occur during the production process, determining whether they can meet specifications and performance, while improving overall efficiency and reducing costs. Final cost.
We can provide various PCB testing services, including:
Manual/Visual Inspection: We have experienced PCB inspectors who incorporate manual visual inspection into multiple tests to ensure thorough inspection of PCBs and their components, ensuring product quality.
Microscopic slice examination: The slice examination of a PCB involves cutting the circuit board into thin sections for observation and analysis, in order to identify potential problems and defects.
Slice inspection is usually carried out in the early stages of circuit board manufacturing to ensure timely detection and correction of issues during the design and manufacturing process. This method can check welding, interlayer connections, electrical accuracy, and other issues. When conducting biopsy examinations, a microscope or scanning electron microscope is usually used to observe and analyze the slices.
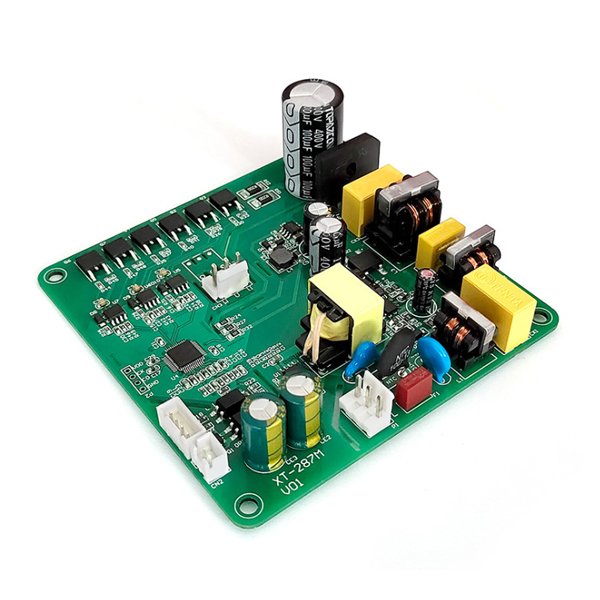
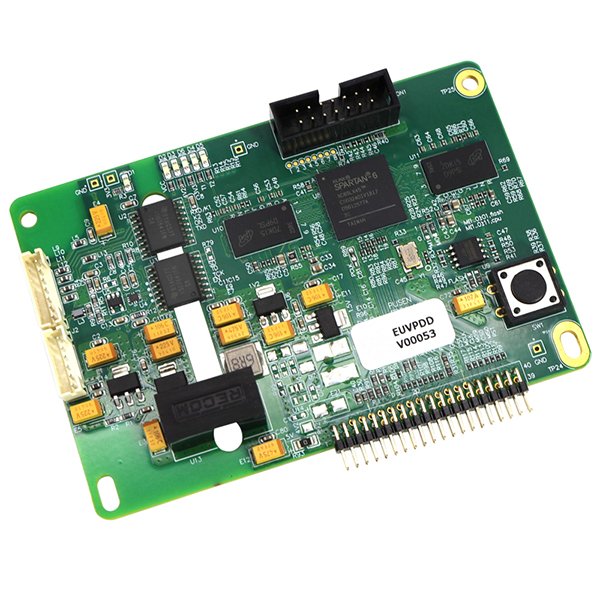
PCB electrical testing: PCB electrical testing can help confirm whether the electrical parameters and performance of the circuit board meet expectations, and can also identify possible defects and problems.
PCB electrical testing usually includes connectivity testing, resistance testing, capacity testing, impedance testing, signal integrity testing, and power consumption testing.
PCB electrical testing can use different testing equipment and methods, such as testing fixtures, digital multimeters, oscilloscopes, spectrum analyzers, etc. The test results will be recorded in the test report for evaluation and adjustment of the circuit board.
AOI Testing: AOI Testing (Automated Optical Inspection) is a method of automatically detecting printed circuit boards through optical means. It can be used to quickly detect defects and problems in the manufacturing process of printed circuit boards, avoid errors in product manufacturing, and improve the quality of printed circuit boards. Reliable quality, reducing failure rates, and improving manufacturing efficiency and product yield.
In AOI testing, specific detection devices such as high-resolution cameras, light sources, and image processing software are used to scan and capture images of the manufactured PCB, and then the captured images are compared with the preset template. Yes, to automatically detect possible defects and issues, including solder joints, components, short circuits and open circuits, accuracy, surface defects, etc.
ICT: In Circuit Test is used to test the electronic components and circuit connection performance on a circuit board. ICT testing can be conducted at different stages of PCB production, such as after PCB manufacturing, before or after component installation, to promptly identify and correct problems on the circuit board and handle them in a timely manner.
ICT testing uses specialized testing equipment and software to automatically test electronic components and connectors on PCBs. The testing equipment contacts the test points on the circuit board through probes and clamps to detect the electrical characteristics of electronic components on the circuit board, such as resistors, capacitors, inductors, transistors, etc. It is also possible to test the circuit board to ensure that its electrical connections operate as designed.
Flying Needle Test: Flying Needle Test uses an automatic probe system to test the circuit connections and functions on a PCB. This testing method does not require expensive testing fixtures and programming time, but instead uses movable probes to contact the PCB surface to test circuit connectivity and other parameters.
Flying needle testing is a non-contact testing technique that can test any area of a circuit board, including small and dense circuit boards. The advantages of this testing method are low testing cost, short testing time, ease of flexible circuit design changes, and fast sample testing.
Functional circuit testing: Functional circuit testing is a method of conducting functional testing on a PCB to verify whether its design meets specifications and requirements. It is a comprehensive testing method that can be used to check the performance, signal quality, circuit connectivity, and other functions of PCBs.
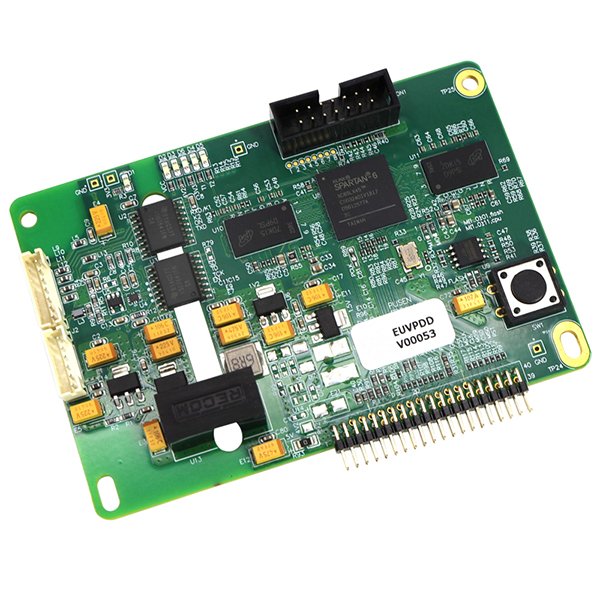
Functional circuit testing is usually conducted after the PCB wiring is completed, using testing fixtures and testing programs to simulate the actual working conditions of the PCB and test its response under different working modes. The testing program can be implemented through software programming, which can test various functions of the PCB, including input/output, timing, power supply voltage, current and other parameters. At the same time, this page can detect many potential issues with PCBs, such as short circuits, open circuits, incorrect connections, etc., and can promptly detect and repair these issues to ensure the performance and reliability of PCBs.
Functional circuit testing is a customized testing method that requires programming and testing fixture design for each PCB. Therefore, the cost is relatively high, but it can provide more comprehensive, accurate, and reliable test results.